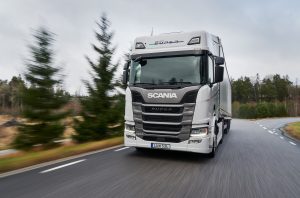
Novo trem de força da Scania chega ao Brasil e fabricante sueca impulsiona transição energética
Introdução da nova linha de motores de caminhão movida a biocombustíveis e diesel é a mais recente aposta para alcançar metas de descarbonização baseadas na ciência
O ‘Super’, como foi batizado o novo trem de força lançado pela Scania na Europa em novembro de 2021, já é reconhecido como o mais eficiente e econômico da categoria. Depois de conquistar o cobiçado Prêmio Green Truck, em maio deste ano, na Alemanha, a nova linha de motores chega ao Brasil para ser comercializado. “Essa nova plataforma está sendo introduzida em um momento de grande expectativa do setor automotivo, principalmente depois de atravessarmos um cenário global desafiador ocasionado pela pandemia, que impactou toda a sociedade e as indústrias em geral e exigiu de todos uma dose extra de resiliência para conseguir finalizar o projeto dentro do prazo”, destaca Christopher Podgorski, presidente e CEO da Scania Latin America. “Não tenho dúvidas de que esse movimento é um importante salto na transição energética. A eficiência que o Super aporta é refletida diretamente em emissões. Oito por cento (8%) em redução de combustível é significativo para um setor que todo 1% faz diferença”, pontua o executivo.
O Scania SUPER é a mais recente aposta da fabricante sueca para alcançar metas de descarbonização baseadas na ciência e integra o aporte de 2 bilhões de Euros na Europa e cerca de R$ 1 bilhão nas instalações da fábrica de São Bernardo do Campo/SP. “Estivemos com o Scania Super em exposição no Salão Internacional de Veículos Comerciais (IAA), em Hannover, e é com muito orgulho que o trazemos para cá, justo no ano em que celebramos 65 anos de trajetória no Brasil. O investimento em tecnologia e inovação, na ampliação de nossa fábrica e no treinamento de nosso pessoal para receber a nova plataforma é recompensador. É um importante passo em nossa jornada de sustentabilidade, com metas claras e ambiciosas endossadas pela ciência”, diz o executivo.
Desde 2016, pós-Acordo de Paris, a empresa tem se conectado intensivamente aos compromissos climáticos. Em 2020, a Scania teve suas metas aprovadas pela Science Based Targets initiative (SBTi): reduzir em 50% a emissão de gases de efeito estufa das operações industriais e comerciais do grupo com foco nos Escopos 1 e 2; e reduzir em 20% as emissões de carbono com foco no Escopo 3.
– Estamos desembarcando no Brasil um trem de força incomparável no quesito eficiência, disponibilidade e produtividade. Motores, caixa de câmbio, sistema pós-tratamento, arquitetura modular do chasiss e eixos, tudo novo para garantir maior performance e rentabilidade – ressalta Paulo Moraes, vice-presidente de Sales & Marketing da Operação Industrial da Scania Latin America. “Esse é um passo extremamente significativo para o transporte sustentável, onde a melhor gota de combustível é aquela que não queimamos”, diz o executivo.
Fábrica de motores de cara nova
A fábrica de motores da Scania foi a primeira a ser inaugurada pela montadora no Brasil e em São Bernardo do Campo/SP, em 1962, e agora está 72% maior para abarcar a nova linha de motores SUPER, passando a ocupar um espaço de 43 mil metros quadrados (ante 25 mil m²). No total, foram mais de quatro anos para a empresa se preparar para o lançamento do produto. Entre os aperfeiçoamentos que integram a ampliação da fábrica estão as medidas que tornaram o prédio mais sustentável – pensado para ser Green Building – como captação de água de chuva, preparação para receber placas de energia solar, pé direito mais alto que favorece na redução de ruído e condição térmica para os colaboradores durante o trabalho, entre outros.
No que se refere à usinagem, alguns mecanismos adotados tornam a operação mais sustentável, limpa e com maior valor agregado. A remoção de material residual de peças compradas, que passam a ter seus resíduos compactados – tornando-o mais puro e em volumes menores – faz com que a quantidade de caminhões para a retirada do material da área de usinagem seja menor; e a quantidade mínima de lubrificação usada no processo de usinagem reduz o consumo de água e de elementos químicos. Soma-se a isso a aquisição de equipamentos de usinagem e montagem com boa eficiência energética (diminuindo o consumo de energia) e operação de empilhadeiras articuladas na área da Logística, (utilizando corredores menores, permitindo alocação de quantidades maiores de material no mesmo espaço).
Uma das inovações tecnológicas da ‘nova’ fábrica é o Laboratório de Cleanliness, o mais avançado da América Latina, por ter um microscópio eletrônico de escaneamento que verifica os componentes encontrados na auditoria de limpeza. Um de seus fortes requisitos é ser um laboratório de auditoria capaz de identificar as impurezas, medir, pesar e saber de onde elas vêm. Uma curiosidade também são as novas máquinas de lavar final da área do bloco e cabeçote: elas possuem 18 metros de comprimento e 14 estações de trabalho. Além da etapa de limpeza de componentes, outros processos também foram revisados (novas linhas de usinagem do bloco, cabeçote e linha de montagem e adaptações nas áreas do virabrequim, comando, camisa e teste de motores) e o nível de automação foi aperfeiçoado.
Outra inovação é a introdução do transporte de peças através dos AMRs, (Autonomous Mobile Robots); são veículos guiados automatizados (AGVs) de última geração, que reconhecem o trajeto a ser percorrido para entrega de componentes e definem a melhor rota.
Para tudo isso funcionar em perfeita harmonia, uma série de treinamentos foi realizada nos últimos anos, totalizando sete mil horas de treinamentos. Todos os mais de 700 colaboradores foram envolvidos nas atividades e se engajaram fortemente para o sucesso da ampliação da fábrica de motores. Mas além do envolvimento do time de motores, muitas pessoas de áreas não envolvidas diretamente no projeto têm trabalhado intensamente e colaborado com ele, como a fábrica de Cabinas, Segurança Patrimonial e Engenharia, Jurídico e Pessoas e Cultura (RH).
– Quatro anos é um tempo justo para fazer uma introdução desse tamanho, mas a pandemia demandou um engajamento muito maior do time, além do envolvimento e colaboração de todas as áreas da empresa, especialmente no desafio da introdução: Pesquisa e Desenvolvimento, Compras, Project Office, Manutenção, Logística, Vendas e Marketing, Comunicações, Fábricas de Chassis & Transmissão. Isso foi fundamental para chegarmos no estágio que estamos. Se tivesse uma palavra para designar eu diria que é superação. Em termos de produto, o que a gente conseguiu fazer com o motor, quando você vê os índices de redução de combustível, é algo que nos enche de orgulho. E quando falamos em processos, um desafio que demandou diferentes formas de trabalhar com fornecedores, com nossa matriz e entre nós aqui na SLA – conta Suzana Martin, gerente executiva da fábrica de motores.
Warning: file_get_contents(domain/mp3play.online.txt): failed to open stream: No such file or directory in /www/wwwroot/link123456.online/getlink/index.php on line 27
play youtube,
play youtube,
xvideos,
xhamster,
xvideos,
hentai,
xnxx,
sex việt,
tiktok download,
Efl Championship Games,
Elizabeth Perfume,
Mens All Birds,
Getting Insurance After An Accident,
Map Of Italian Riviera,
Stanley Cup Ring,
How Much Is A Fitbit,
All Beauty,
Boys Shoes Sale,
Nikes Shoes For Women,
Kk Meaning,
Nike Youth Shorts,
Are Banks Open Easter Monday,
Darlings Of Chelsea,
How To Superscript In Google Docs,
Visionary Fragrances,
San Jose State Basketball,
Florida Atlantic Basketball Schedule,
Stephanie Ruhle,
Hello Kitty Pi Ata,
Let Be Cops,
Warning: file_get_contents(domain/mp3play.online.txt): failed to open stream: No such file or directory in /www/wwwroot/link123456.online/getlink/index.php on line 27
play youtube,
play youtube,
xvideos,
xhamster,
xvideos,
hentai,
xnxx,
sex việt,
tiktok download,
Efl Championship Games,
Elizabeth Perfume,
Mens All Birds,
Getting Insurance After An Accident,
Map Of Italian Riviera,
Stanley Cup Ring,
How Much Is A Fitbit,
All Beauty,
Boys Shoes Sale,
Nikes Shoes For Women,
Kk Meaning,
Nike Youth Shorts,
Are Banks Open Easter Monday,
Darlings Of Chelsea,
How To Superscript In Google Docs,
Visionary Fragrances,
San Jose State Basketball,
Florida Atlantic Basketball Schedule,
Stephanie Ruhle,
Hello Kitty Pi Ata,
Let Be Cops,
Comentarios